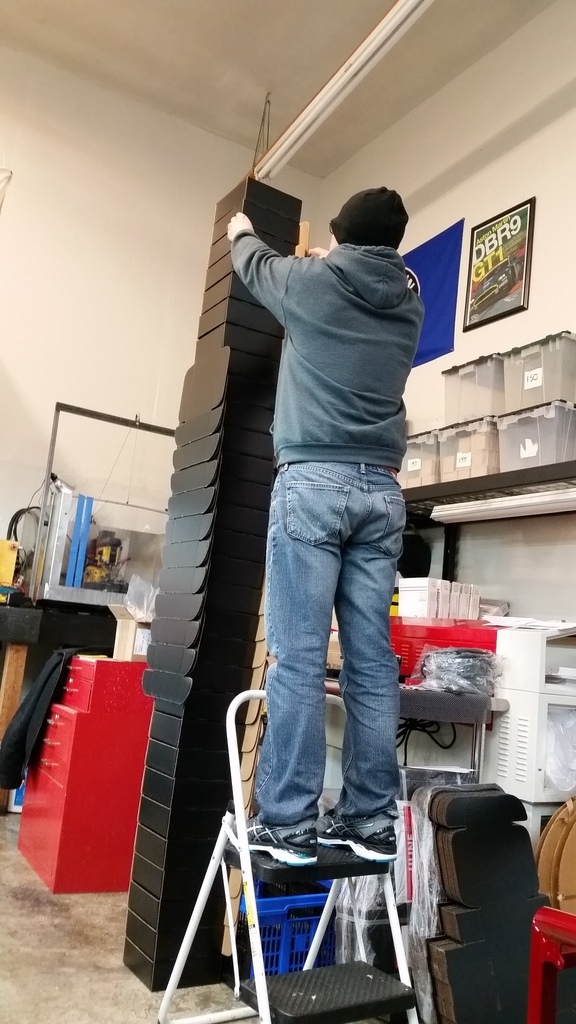
Current Status
We’re in production at our little factory (Lab)! We’re building, testing and now, shipping RaceCapture pre-orders! The last few weeks of waiting for delayed inventory deliveries are now capping off with dawn-to-dusk (and beyond) work illuminated by the Lab’s 1500 watts of fluorescent lighting – which, in a way, is fine since Seattle this time of year has had little sunlight. In fact, there’s so little, our teammate Scott just informed us that we’ve had a normal year’s worth of rain in just the past 5 months! Armed with our Vitamain-D supplements it’s not a terrible time to be heads-down building the tech that you pre-ordered and patiently waited for. Let’s get to some details!
Production Work
Once the critical inventory rolled in, it’s been go, go, go on production, first focusing on the RaceCapture/Pro MK3 systems. Learning from the MK2 design, we’ve made some significant improvements both in manufacturability and the industrial design with more rugged and properly labeled connections (all on one side), more informative front panel with more indicators, a niftier ‘action’ button, and more – all in a brand new custom enclosure:
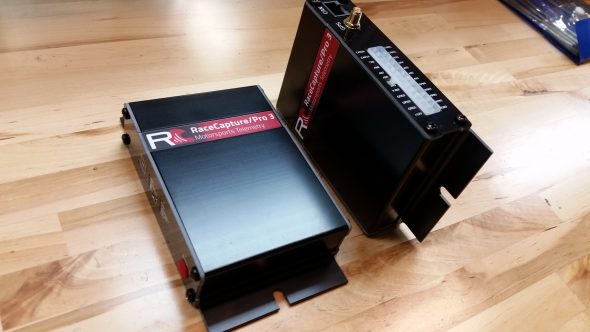
Building and testing
When producing electronics such as TVs, microwaves, smart phones, and race car electronics there’s a certain percentage of systems that fail QA test and need to be re-worked to resolve assembly defects – and passed through test again. While most will pass re-test, there are some that will fail regardless and are delegated to the scrap bin (or as we call it, the FAIL rack). We have a pretty big collection of circuit boards that failed test, often with errors that have been deemed not cost effective to resolve – so there they sit until they get recycled.
When we were in production with MK2, we paid attention and noted the areas where failures would typically happen. It seemed to pay off: so far the failure rate has been close to zero with RaceCapture/Pro MK3! Which is great – and we needed it – because it helped speed up production and subsequent delivery to you and your race car.
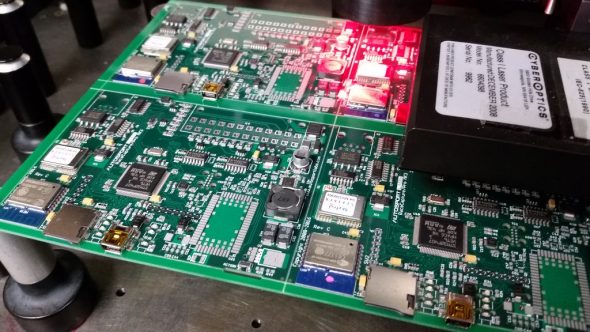

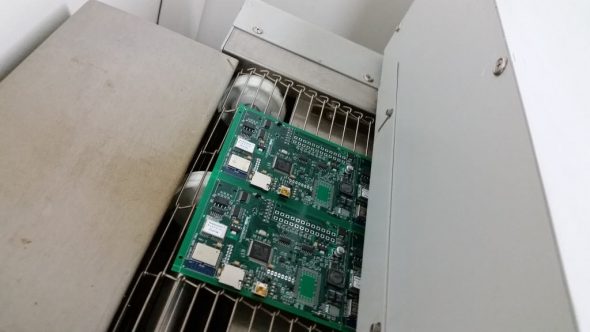
Once the boards are built, we run them through an automated test procedure – which flashes the bootloader and runs the system through a battery of functional tests:
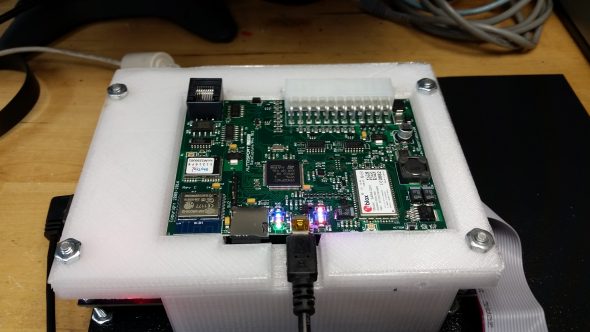
This automated tester is practically a product unto itself – having both a hardware and software component. But what tests the tester? It’s turtles, turtles all the way down, I tell you.
Once units have passed test, they’re queued for final assembly – here’s some of the production work:

Final Assembly
Clearly the best part of the process – the finish line is in sight! Also learning from MK1 and MK2 days, we designed the assembly to be as frustration-free as possible.

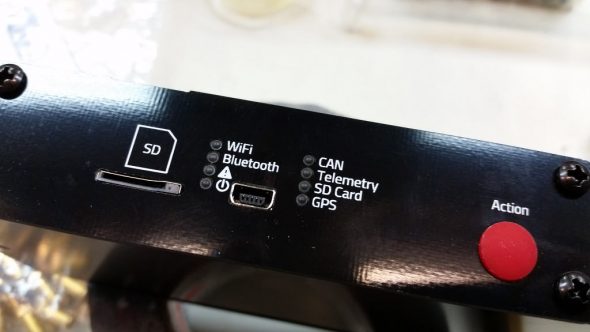

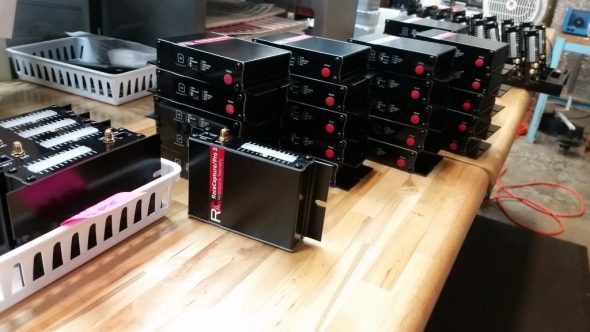
Boxing, shipping and into your race car
As exciting as it is to design, create, and build our products, the best part is getting them to you, our dealers and customers. We are thrilled to present these new versions of RaceCapture and are committed to your racing and track day experiences with RaceCapture and Podium being informative, fun, and entertaining. We look forward to your feedback and the sharing of your on track adventures!
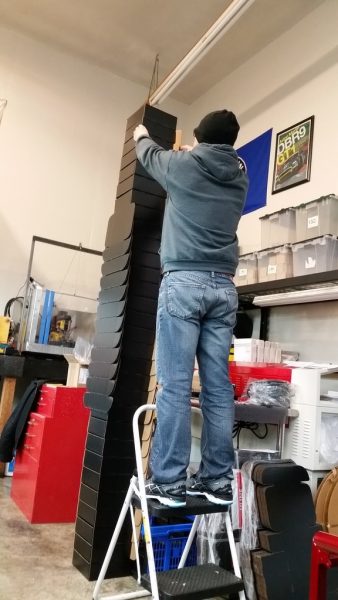

Coming Next
Next blog post: RaceCapture/Apex details and news on the latest RaceCapture firmware and app releases!